Introduction to CIP for Anvil Foundry
Clean Set up (CIP) for Iron block Foundry is a crucial cycle that ensures the productivity and life span of preparing hardware. On the off chance that you’re a homebrewer or a specialist brewer utilizing a Blacksmith’s iron Foundry framework, understanding CIP is basic for keeping up with the nature of your blends and the wellbeing of your equipment. Via robotizing the cleaning system, CIP saves time while guaranteeing reliable sterilization, diminishing the gamble of defilement, and working on generally speaking execution.
The blending system frequently abandons buildup, including bounces, malt sugars, and yeast. Without legitimate cleaning, these deposits can hold onto microorganisms and effect the flavor profile of your next clump. CIP is a definitive answer for address these difficulties effectively, permitting you to zero in on creating extraordinary brews while keeping up with elevated expectations of cleanliness.
Why CIP Matters for Anvil Foundry Equipment
Cleaning your Iron block Foundry fermenting framework routinely and really is essential in light of multiple factors:
- Maintains Brewing Quality: Residue buildup can lead to off-flavors and spoilage, directly impacting the quality of your beer.
- Prevents Contamination: Appropriate CIP kills destructive microscopic organisms and microorganisms that can demolish your mix.
- Extends Equipment Lifespan: Ordinary cleaning forestalls erosion and mechanical wear, guaranteeing your Blacksmith’s iron Foundry framework endures longer.
- Saves Time and Effort: Computerized or semi-robotized cleaning decreases physical work, permitting you to zero in on preparing.
- Compliance with Standards: For proficient brewers, CIP guarantees consistence with sanitation and industry guidelines.
- Cost Efficiency: Long haul investment funds through diminished hardware fixes and substitutions.
How CIP Works: A Step-by-Step Breakdown
Implementing CIP for your Anvil Foundry involves a systematic process designed for thorough cleaning. Here’s how it works:
- Preparation:
- Drain any leftover liquid from the brewing system.
- Disassemble removable parts if needed.
- Inspect the equipment for visible residue or damage before proceeding.
- Pre-Rinse Cycle:
- Use warm water to remove loose debris and residue.
- This step ensures that the cleaning agents work effectively by eliminating surface particles.
- Chemical Cleaning:
- Circulate an alkaline cleaning solution through the system to break down organic residue such as malt sugars and proteins.
- Allow the solution to contact all surfaces for the recommended duration.
- Intermediate Rinse:
- Rinse the system with clean water to remove residual cleaning agents.
- Use pH test strips to confirm that the system is free of chemical residues.
- Acid Rinse (Optional):
- Use an acid solution to remove mineral deposits and prevent scaling.
- This step is particularly useful in areas with hard water.
- Ensure thorough rinsing after the acid rinse to avoid any residual acidity.
- Final Rinse:
- Rinse with clean, potable water to ensure no chemical residues remain.
- Check pH levels to confirm cleanliness and safety.
- Sanitization:
- Circulate a sanitizing agent to eliminate any remaining microorganisms.
- Allow the system to air dry before the next use, preventing moisture-related issues.
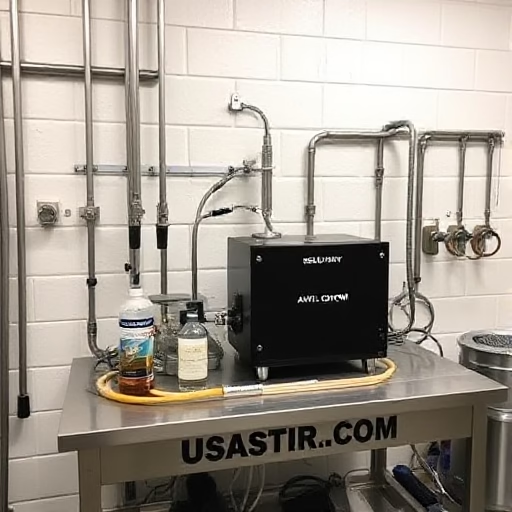
Benefits of Using CIP for Anvil Foundry
Adopting CIP for your Anvil Foundry system provides several advantages:
- Consistency: Ensures thorough cleaning every time without human error.
- Efficiency: Reduces downtime between brewing cycles, maximizing productivity.
- Safety: Minimizes exposure to harmful cleaning chemicals by automating the process.
- Cost-Effective: Saves money in the long run by reducing the need for frequent replacements or repairs.
- Enhanced Performance: Clean equipment leads to better heat transfer and improved brewing efficiency.
- Scalability: Ideal for both small-scale homebrewers and large-scale operations.
Essential Tools and Cleaning Agents for CIP
For an effective CIP process, you’ll need specific tools and cleaning agents designed for brewing equipment:
- CIP Pumps: Facilitate the circulation of cleaning solutions, ensuring thorough contact.
- Alkaline Cleaners: Remove organic residues like malt sugars and proteins.
- Acid Cleaners: Eliminate mineral deposits and scale buildup.
- Sanitizers: Ensure the system is free from microorganisms before brewing.
- pH Test Strips: Verify the effectiveness of rinsing and sanitization by measuring residual acidity or alkalinity.
- Tubing Brushes: For manual cleaning of hard-to-reach areas, like hoses and valves.
- Thermometers: Monitor cleaning solution temperatures for optimal effectiveness.
- Personal Protective Equipment (PPE): Gloves and goggles to ensure safety during the cleaning process.
Common Challenges and How to Overcome Them
While CIP is highly effective, some challenges may arise:
- Inadequate Rinsing:
- Problem: Residual cleaning agents can affect brewing quality.
- Solution: Use sufficient water volume and check pH levels to ensure proper rinsing.
- Chemical Residue:
- Problem: Leftover chemicals can be hazardous.
- Solution: Opt for food-safe cleaning agents and conduct multiple rinses if needed.
- System Blockages:
- Problem: Hoses and valves can get clogged with residue.
- Solution: Regularly inspect and clean hoses, filters, and other components to prevent clogging.
- Scaling and Hard Water Issues:
- Problem: Mineral deposits can reduce equipment efficiency.
- Solution: Use acid cleaners periodically to remove scale buildup and ensure proper heat transfer.
- High Cleaning Costs:
- Problem: Frequent cleaning can become expensive.
- Solution: Invest in reusable cleaning agents and efficient CIP pumps to reduce overall costs.
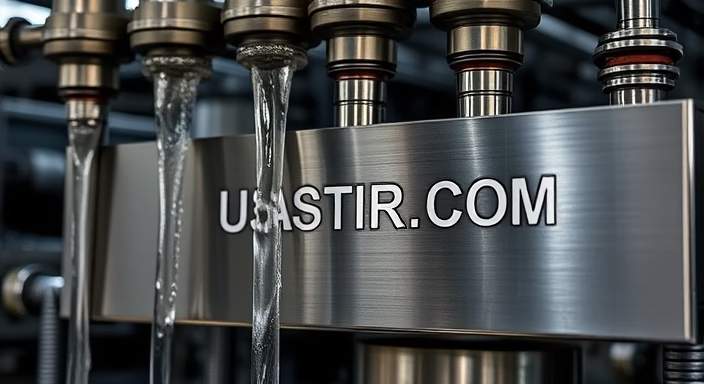
FAQs About CIP for Anvil Foundry
- What is the ideal frequency for CIP?
- Perform CIP after every brewing cycle or as needed based on residue buildup.
- Can I use household cleaners for CIP?
- No, always use food-grade cleaning agents designed for brewing equipment to ensure safety and effectiveness.
- How long does a CIP cycle take?
- A complete CIP cycle typically takes 30-60 minutes, depending on the system’s size and condition.
- Do I need specialized equipment for CIP?
- While not mandatory, using CIP pumps and tanks improves efficiency and results.
- What temperature should cleaning solutions be?
- Alkaline solutions work best between 120-140°F, while acid solutions perform optimally between 110-130°F.
Tips for Optimizing CIP for Anvil Foundry
- Monitor Temperature: Ensure cleaning solutions are at the optimal temperature for maximum effectiveness.
- Follow Manufacturer Guidelines: Refer to the Anvil Foundry manual for specific cleaning instructions and recommendations.
- Document Cleaning Cycles: Maintain a log to track cleaning frequency, effectiveness, and any issues encountered.
- Invest in Quality Products: High-quality cleaning agents and tools deliver better results and protect your equipment.
- Train Your Team: Ensure all users are familiar with CIP procedures to maintain consistency and efficiency.
- Inspect Regularly: Check for wear and tear on hoses, gaskets, and other components to prevent malfunctions.
Key Takeaways
At this point, obviously CIP is a distinct advantage for keeping up with your Blacksmith’s iron Foundry framework. It guarantees the greatest brews as well as saves time, exertion, and cash over the long haul. With steady cleaning rehearses and the right instruments, you can forestall pollution, improve blending proficiency, and broaden the life expectancy of your gear. Whether you’re a carefully prepared brewer or simply beginning, integrating CIP into your routine is an interest in your fermenting achievement.
Conclusion: Ready to Simplify Your Brewing Process?
Don’t let residue and contamination compromise your brewing passion. Embrace CIP for Anvil Foundry and enjoy consistent, high-quality results with every batch. Have questions or tips to share? Leave a comment below and join the brewing community in perfecting the art of beer-making!
Visit Us for more content